Steam Turbine
Fauji Fertilizer
Profiles Woodward 505, CPC II and Protech G2 as a complete solution for Fauji Fertilizer. The customer had reported unacceptable speed fluctuation with the original installed system. As a result of this retrofit the operator has reported improved steam management and the need for less human intervention.
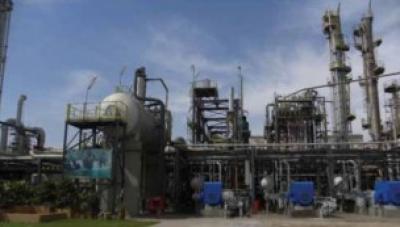
First Farmer
Upgrading both steam turbine and power management controls on a GE double extraction steam turbine allows First Farmer to manage fluctuating grid voltage while exporting power. The Woodward Easygen 3200, 505DE and SPC has made this impressive upgrade in performance possible.
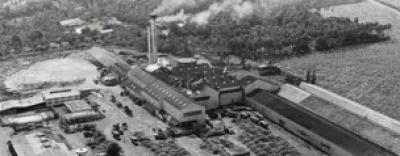
Chandra Asri Petrochemical
Upgrade of Steam Turbines and Anti-surge
Controllers in Petrochemical Plant Improves
Operations and Adds Redundancy
At its Cilegon plant, CAP was constantly facing issues with the availability
of spare parts for its turbine control systems and anti-surge controllers.
These control systems control and protect the Siemens single extraction
steam turbines driving the cracked gas compressor GT/GB-201 and the
propylene compressor GT/GB-501. The GB-201 is a 5-stage compressor
with 2 recycle valves and the GB-501 is a 4-stage compressor with
5 recycle valves. To solve obsolescence issues and improve system
efficiency and reliability, CAP decided to retrofit the turbine control
systems and anti-surge controllers of both compressors to fully redundant
integrated turbine-compressor controls (ITCC).
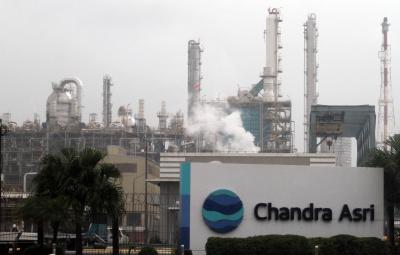
Dian Swastatika Sentosa
DSS Serang was using a GEC Alsthom 87.5 MVA static excitation system for generator #6, which had already been obsolete for a long time and for which Alsthom had been unable to provide spare parts and technical support. To avoid future maintenance problems and - most importantly -
reduce the risk of issue-related downtime, DSS decided to retrofit its GEC Alsthom excitation system.
The company required a system with 100% redundancy in its automatic voltage regulator (AVR) control and power supply; functionalities that were also present on the original Alsthom unit. Furthermore, improvements had to be made to the monitoring system and end-users had to be provided with a solution that was easier to operate.
In short, the objectives of the retrofitting project were to:
- Replace the obsolete system components
- Provide DSS with a better monitoring solution
- Provide end-users with easier operation
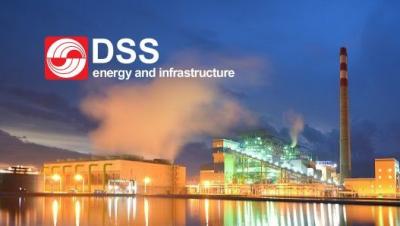
Pupuk Sriwidjaya
The GB-102 compressor is a crucial part of the Pusri 3 fertilizer plant: The application controls the CO2 feed to the fertilizer reactor. Without this CO2 feed the plant is unable to operate and the facility loses its entire production. To ensure the quality of the fertilizer, the CO2 feed has to stay aligned with the feed of other components (ammonia, oxygen, natural gas, etc.) to the fertilizer reactor. Changes in this area require a fast and accurate response of the CO2 feed to optimize and ensure the quality of the end product. Process operators must be able to intervene through process control set points in an accurate, fast, and easy way.
Pusri had previously worked with Compressor Control Company (CCC) on
the installation of CCC�s Series 3 Plus control system for their Borsig GmbH
CO2 compressor. However, in the first year after the commissioning, the
following issues appeared:
- Constant failure of the system�s redundant power supply;
- The redundancy of the system was not able to perform hot backup;
- The CCC control system did not give operators accurate information to
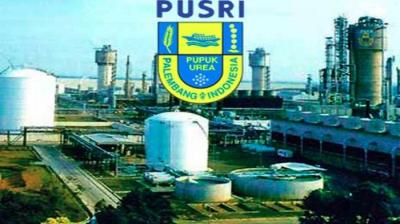